- ユニケミートップ
- Uni-Lab(分析技術情報)
- 摩擦摩耗試験機による トライボロジー特性評価の解説
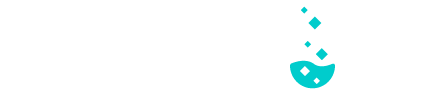
摩擦摩耗試験機による トライボロジー特性評価の解説
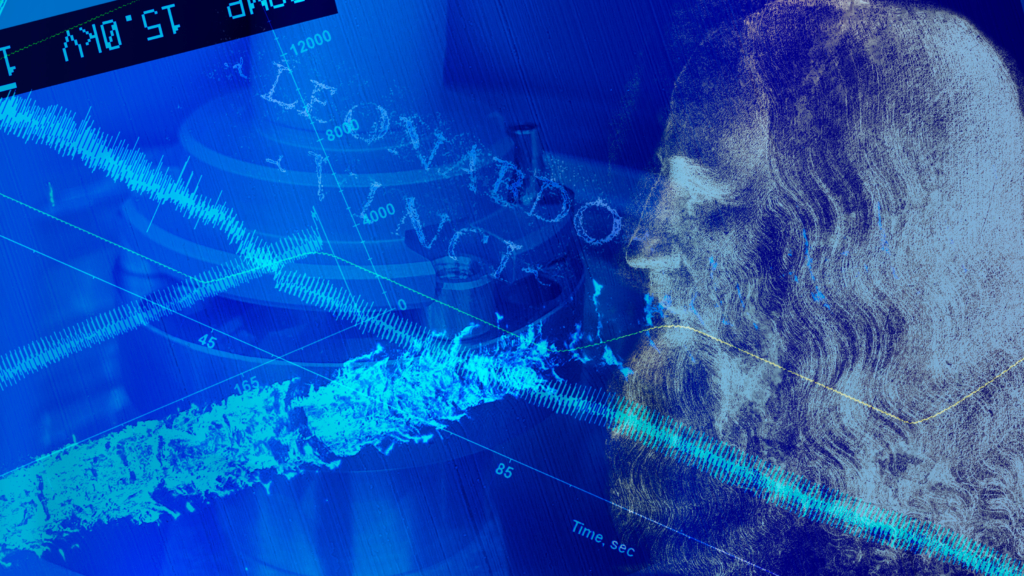
1.はじめに
2050 年のカーボンニュートラル実現に向けた動きが活発になっており、その取り組みの一つとして産業界の様々な分野でエネルギー効率の向上(省エネルギー)が求められている。その重要な役割を果たす技術の一つは、摩擦・摩耗の低減に寄与する「トライボロジー技術」である。あらゆる部品、機械、設備の稼働部に摩擦・摩耗は存在し、エネルギー損失の主たる原因となっている。例えば自動車(ガソリン車)の場合、動力伝達部の摩擦によるエネルギー損失は燃料消費の35%に及ぶとの試算もある1)。トライボロジー技術は、低摩擦化した摺動部品が摩擦損失を低減し、摩耗抑制した製品が長寿命化するなどとモノづくりに活かされて、省エネルギーそのものを期待できる。
当社は、トライボロジー技術の評価に用いる「多機能型摩擦摩耗試験機」を昨年度に導入し、カーボンニュートラルに向けたモノづくりを更に支援することにした。
本稿では、具体的な評価事例を挙げて多機能型摩擦摩耗試験機の特徴を解説する。
2.トライボロジーとは
2.1.定義と歴史
トライボロジーは、ギリシャ語の「tribos:擦る」と「ology:学問」を組み合わせた造語である。
一般には「摩擦学」「摩擦技術」などと簡潔に訳されるが、一般社団法人日本トライボロジー学会では「潤滑、摩擦、摩耗、焼付き、軸受設計を含めた『相対運動しながら互いに影響を及ぼしあう二つの表面の間におこるすべての現象を対象とする科学と技術』」2) と定義している。要するに接する表面間に生じる摩擦と摩耗を、適切に掌握・統制する科学又は技術だといえる。
トライボロジーの歴史は古く、古代エジプトの壁画に、壺から潤滑剤を注いでいる人物が描かれており、記録に残る最初のトライボロジストと言われている。そして、摩擦という現象に初めて科学の光を当てたのは、Leonardo da Vinci(レオナルド・ダ・ヴィンチ)とされ、約500 年前に軸受の基礎となる図画を残している。
近代研究では、18 世紀フランスの物理学者Coulomb(クーロン)により「摩擦の基本法則(アモントン-クーロンの法則)」が確立され、「摩擦の凹凸説」(表面凹凸の引っ掛かりが摩擦の原因とする説)が主流となる。
しかし、次第に矛盾を呈するようになり、20 世紀半ばBowden(バウデン)とTabor(テーバー)により「摩擦の凝着説」(表面接触による凝着のせん断力が摩擦の原因とする説)が提起されて広く認められることになる。
現代になり、その領域はナノレベルの「ナノトライボロジー」や人工関節など生体機能に係る「バイオトライボロジー」などへと発展し研究が進められており、航空・宇宙・自動車・電気・医療・土木・建築等、様々な分野でその技術が活用されている。
2.2.トライボロジーの試験装置
摩擦や摩耗の現象は、試験装置を利用して調査しまたは研究する。試験装置は、静摩擦係数や動摩擦係数を測定する装置例えば滑り出す角度またはトルクを測定して摩擦係数を求める方法の装置のほか、次の①から⑧に例示する摺動の様々な組合せを想定した摩擦・摩耗の試験装置がある。そうした摩耗・摩擦試験装置はトライボロジーの特性の把握に必須であり、材料や表面処理、潤滑剤の選定そして故障解析などに利用する。本稿が紹介する多機能型摩擦摩耗試験機もその一つである。
① 回転ピン(ボール)オンプレート(ディスク)式:固定したボールまたはピンを回転平板に押し当てる方法
② 往復動ピン(ボール)オンプレート(ディスク)式:固定したボールまたはピンを往復動平板に押し当てる方法
③ スラストシリンダ(リングオンディスク)式:回転円筒の端面を平板に押し当てる方法
④ ブロックオンリング式:回転円筒(リング)側面にブロックを押し当てる方法
⑤ 四球式:互いに接するように置いた三つの球に、もう一つの回転する球を押し当てる方法
⑥ ピン・ブロック式:回転するピンを一対のV 字ブロックで挟む方法
⑦ ローラー式:二つの回転するローラーを互いに押し当てる方法
⑧ スクラッチ試験:とがったピンなどを往復動平板に押し当てる方法
3.多機能型摩擦摩耗試験機
3.1.試験機の構造
多機能型摩擦摩耗試験機(写真1)は、回転や往復など試験形態を決めるドライブ(写真2)、摩擦力やトルクを測定するセンサー(写真3)から構成される。これにピン、ボール、リング、ディスク、プレートなど相対する「試験材」と「相手材」(写真4)を組合せ、摺動摩擦させて次節の試験データを得る。
ドライブとセンサーを交換すれば、回転摺動試験、往復摺動試験、スクラッチ試験など異なる試験形態に対応可能である。また、試験材と相手材の形状により、ボールオンプレート、ピンオンプレート、リングオンディスク(通称スラストシリンダ式、鈴木式とも呼ばれる)など、種々の組合せ(図1)を選択できる。低荷重、高荷重など試験条件の切り替えも容易で、様々な条件の試験が速やかに実施可能である。評価対象材料の使用環境や試験形態、評価目的によりこれらを使い分ける。
また試験の摺動等の可動範囲の制約はあるが、専用の治具や固定方法をカスタマイズすれば、テストピースに限らず実装部品も試験可能である。
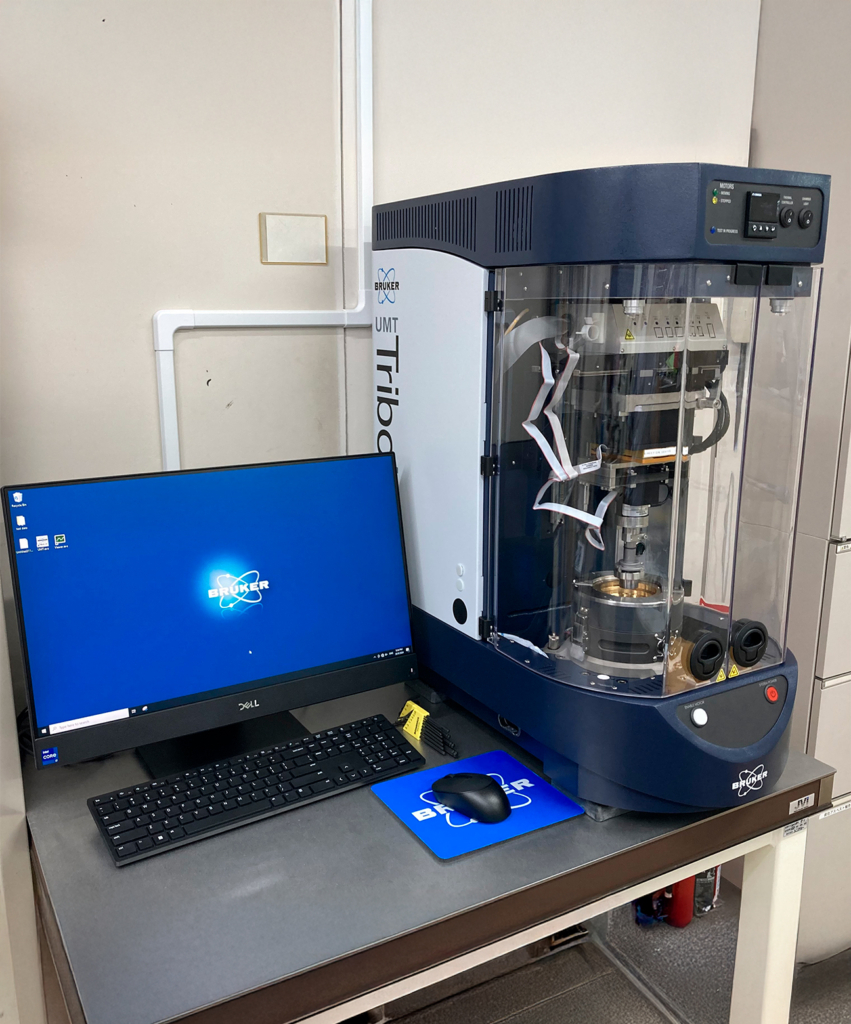
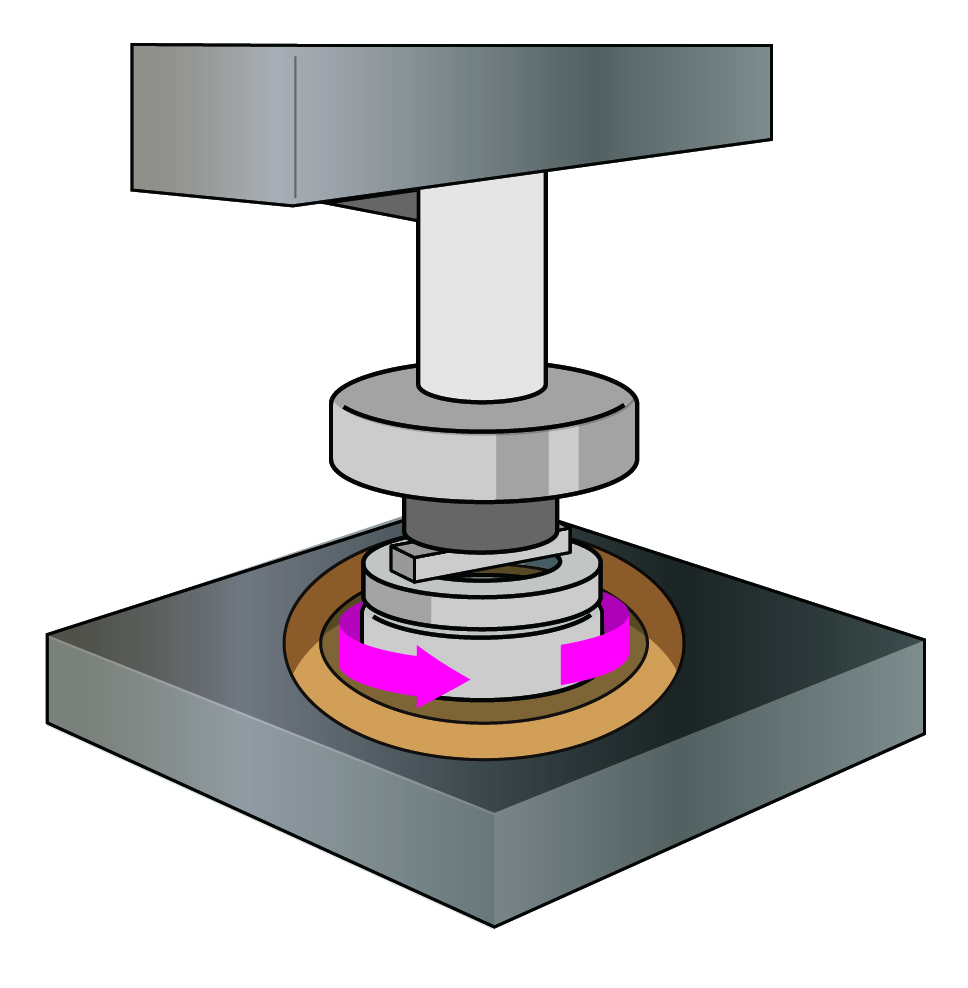
リングオンディスク
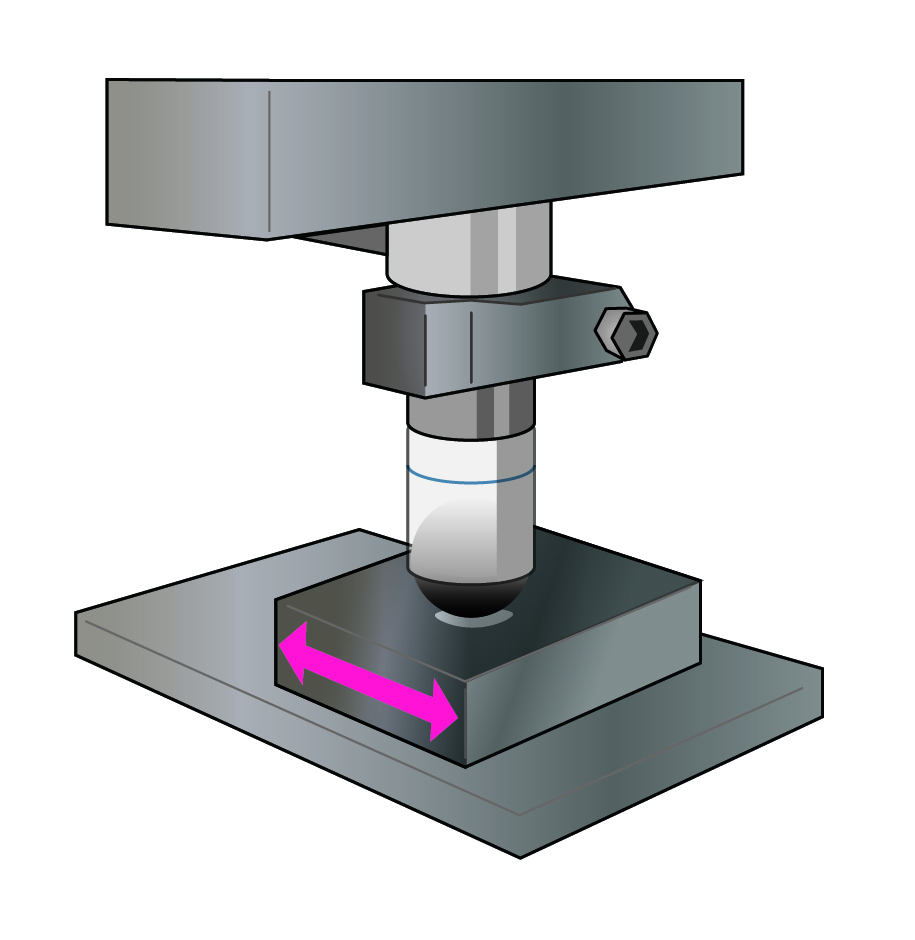
ボールオンプレート
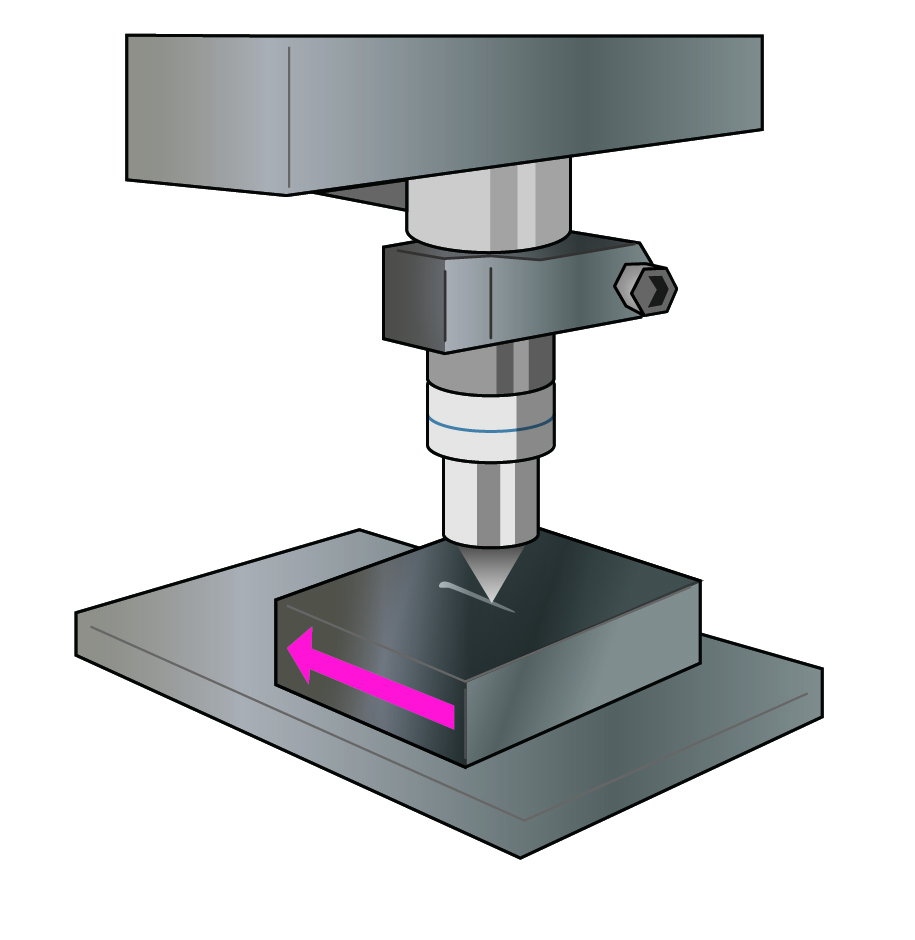
ピンオンプレート
図1 試験形態の例(イメージ)

写真2 ドライブ


写真3 センサー




写真4 試験材と相手材の例

3.2.試験データ
多機能型摩擦摩耗試験から得られる試験データは次のとおり。
① 摩擦力
摺動する2 物体間に生じる抵抗力を指し、静摩擦力と動摩擦力に分けられる。静摩擦力は停止した状態の物体が動き出す時に生じる力で、動摩擦力は物体が動いている時に生じる力である。
② 摩擦係数
2 物体間の滑りやすさを表す指標であり、摩擦力を同じ単位の荷重で除した値であるため単位が無い(無次元量)。静摩擦係数、動摩擦係数がある。
③ 摩耗
摩擦により固体表面の減量する現象をいう。評価項目に、摩耗量(重量変化)、摩耗状態(形状変化)、被膜の剥離荷重などがある。
ただし、これらの試験データはある試験条件下で得られる測定値であって、材料の固有値とならないことに留意する必要がある。
4.トライボロジー特性評価
トライボロジー特性を評価するには、トライボロジーに関する課題や問題を抱えている製品の摺動部に着目し、摺動条件を模した摩擦摩耗試験を行う必要がある。そして得られた試験データから課題や問題の解決策を検討する。
本章では、3 種類の試験形態(回転摺動試験、往復摺動試験、スクラッチ試験)について、その概要と模擬試験による評価事例を紹介する。
模擬試験は、鋼材(S45C:Ra 0.2 μm 以下)に硬質被膜(DLC:ダイヤモンドライクカーボン)を施したテストピースを作製し行った。試験形態毎の評価対象と評価項目を表1 に示す。
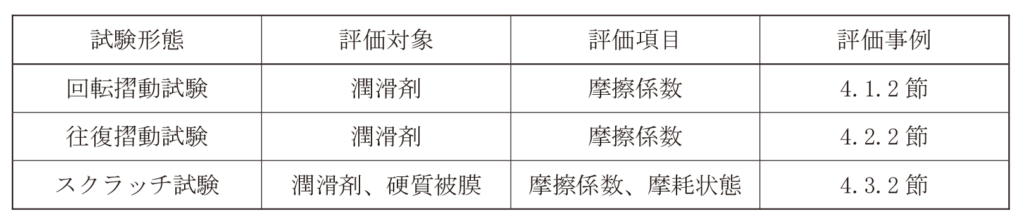
4.1 回転摺動試験
4.1.1 概要
回転摺動試験は、固定したプレート(もしくはディスク)とボール、または回転軸が同じリングとの間の回転摺動による摩擦と摩耗を測定する。セラミックス、金属、樹脂、ゴム、オイルや潤滑剤など多種多様な材料の試験が可能である。プレートとボールの場合点接触のため、摩耗の進行に伴い接触面積が拡大し面圧の変化を生じるものの、片当たりが起き難い。プレートとリングの場合面接触のため、摩耗が進行しても接触面積に変化がない一方、片当たりの発生が多い。面圧変化と片当たりはいずれも測定精度に影響する。ちなみに模擬試験を実施した多機能型摩擦摩耗試験機はセルフレベリング機構が備わっており、片当たりの軽減が可能である。
回転摺動試験は、高温高荷重で作動する軸受け等の金属部品を対象に焼き付き荷重の評価に利用し、そして『JIS K 7218 :1986, プラスチックの滑り摩耗試験方法』の試験方法に採用されている。
4.1.2 評価事例
テストピースに評価用の潤滑剤を塗布し、相手材をリング(S45C)、回転数100 rpm、荷重を10 N から100 N まで段階的に増し、摩擦係数の推移を評価した結果を図2に示す。潤滑剤は荷重が増加しても低い摩擦係数を維持しており、上記荷重範囲内の摩擦特性が良好と判断できる。
同一条件で複数の潤滑剤を試験すれば、摩擦係数の高低、摩擦係数が上がるまでの荷重の差異から、潤滑剤の滑りやすさや耐久性などの性能を比較評価できる。
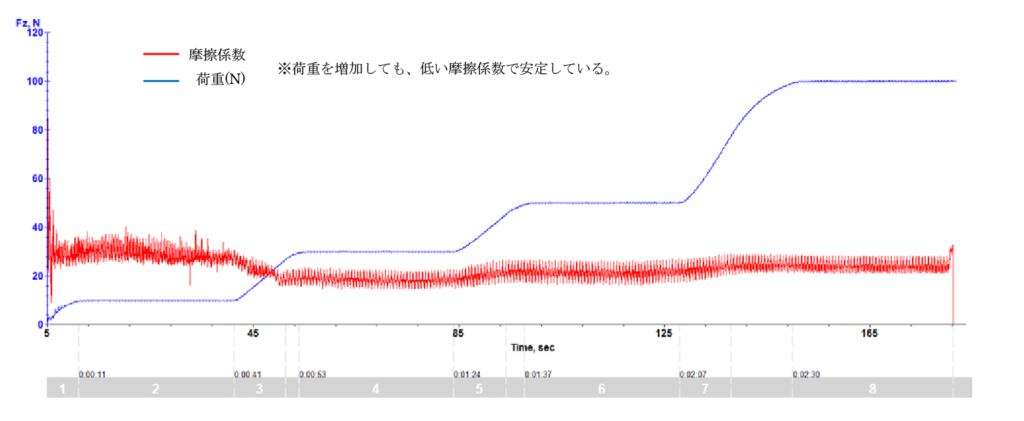
4.2 往復摺動試験
4.2.1 概要
往復摺動試験は、固定したプレートとピンまたはボール間の往復摺動による摩擦及び摩耗を測定する。回転摺動試験と同様に様々な材料に対応可能である。摩擦力測定を行う場合片当たりの影響を低減するため、ボールを使うことが多い。
4.2.2 評価事例
テストピースに比較評価用の潤滑剤1 及び2 を塗布し、相手材をφ 6.3 mm SUJ-2 ボール、荷重10 N、速度1.3 mm/s の条件で摩擦係数を測定した結果を図3に示す。潤滑剤2 は潤滑剤1に比べ静摩擦係数、動摩擦係数ともに低い値を示しており、本試験条件下では滑りやすい潤滑剤であると判断される。
ボールサイズ(形状)、荷重、速度を、評価したい潤滑油などの製品の使用環境に近い条件にすれば、製品の摩擦に関する実際的な優劣を判断できる。
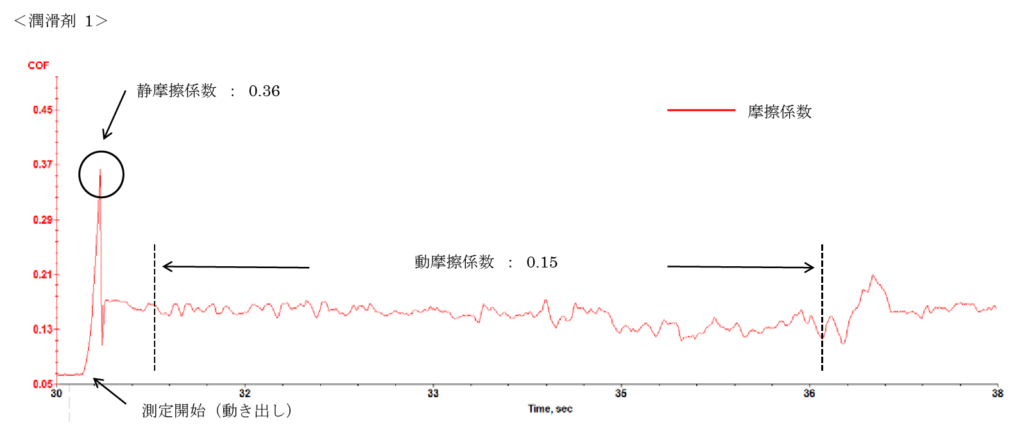
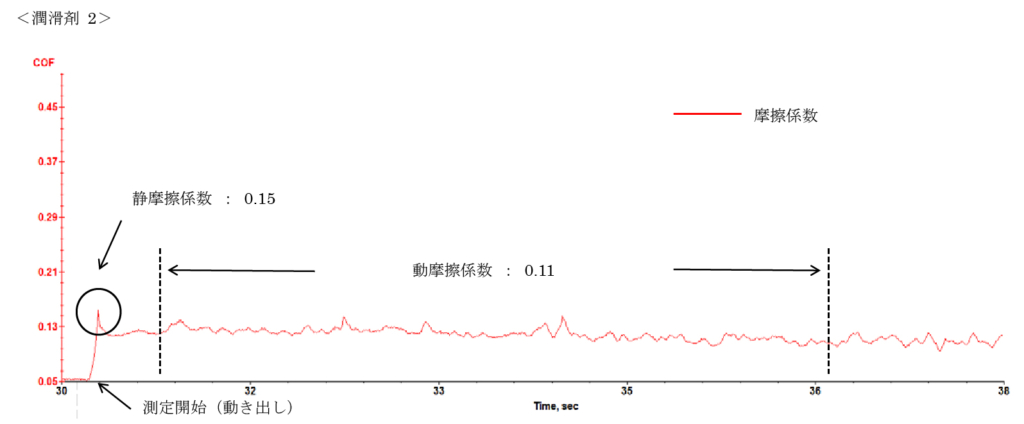
4.3 スクラッチ試験
4.3.1 概要
スクラッチ試験は、一定のまたは逓増する荷重を加え、固定したプレートとピン(圧子)またはボールで材料表面を引っかき、スクラッチ痕(母材露出位置)の顕微鏡観察と合わせて評価を行う。
セラミックス、金属、樹脂や各材料に施された表面処理被膜の耐摩耗性、耐擦傷性、密着強度を調査する。
『JIS K 5600-5-5:1999, 塗料一般試験方法−第5 部:塗膜の機械的性質−第5 節:引っかき硬度(荷重針法)』にも適合する。
4.3.2 評価事例
テストピースに評価用の潤滑剤を塗布し、相手材をダイヤモンド圧子(頂角 120°)、速度1.3 mm/s、移動距離10 mm、荷重を1 N から30 N まで一定の割合で増していき、摩耗特性を測定した結果を図4に示す。
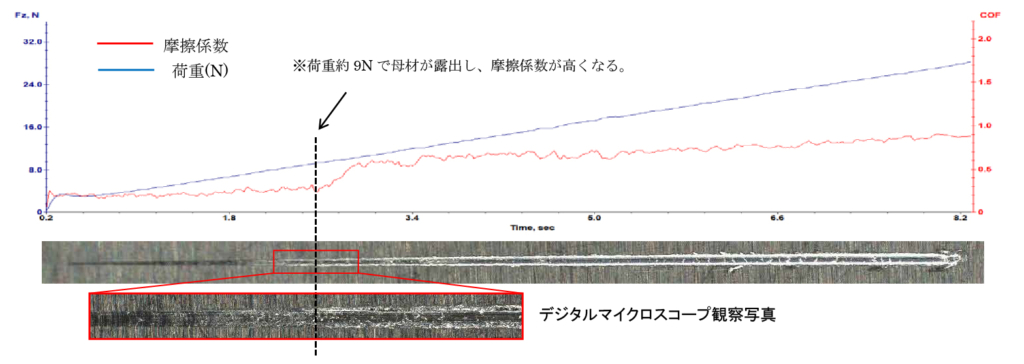
荷重約9 N で摩擦係数が急に高くなり、スクラッチ痕のデジタルマイクロスコープ観察画像から母材の露出が確認できる。この荷重が潤滑剤の耐久性、被膜の耐摩耗性や密着強度の指標となる。
5.その他試験機器による複合評価
摩擦摩耗試験に加え、元素分析や粗さ測定など異なるアプローチの試験方法を併用すれば、トライボロジー特性を多角的な視点で解析できる。他の試験方法とその測定事例を以下に示す。
① SEM(走査型電子顕微鏡)やEPMA(電子線マイクロアナライザー)を用いた摩擦面の観察や元素分析。
EPMA による元素分析(面分析)は、目視で確認できない被膜や潤滑剤成分の有無及び多寡を観測できるため、摩擦係数の高低及び推移の根拠を示すデータとなり得る。(図5)
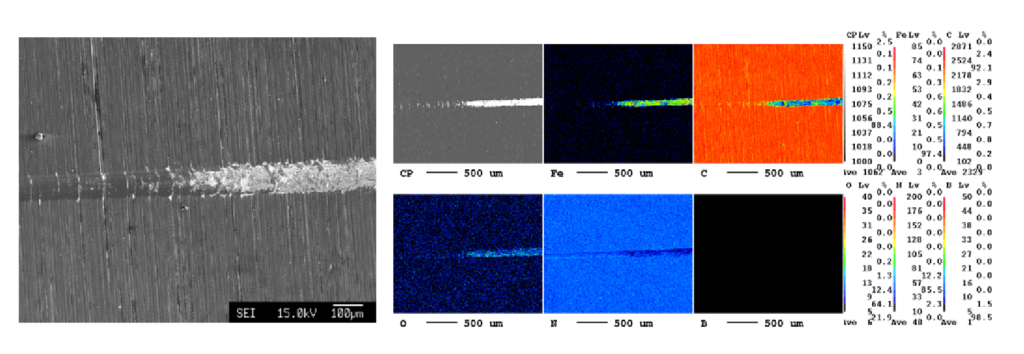
・母材露出部のSEM 画像とEPMA による面分析結果。
・ 母材露出部から母材成分のFe(鉄)が多く検出されるが、硬質被膜成分のC(炭素)も検出されている。
残存する被膜の潤滑性が、摩擦係数の急増緩和に寄与していると考えられる。
② 非接触三次元粗さ計を用いた摩擦面の形状及び摩耗深さ測定。
摩耗深さから摩耗量を把握できる。(図6)
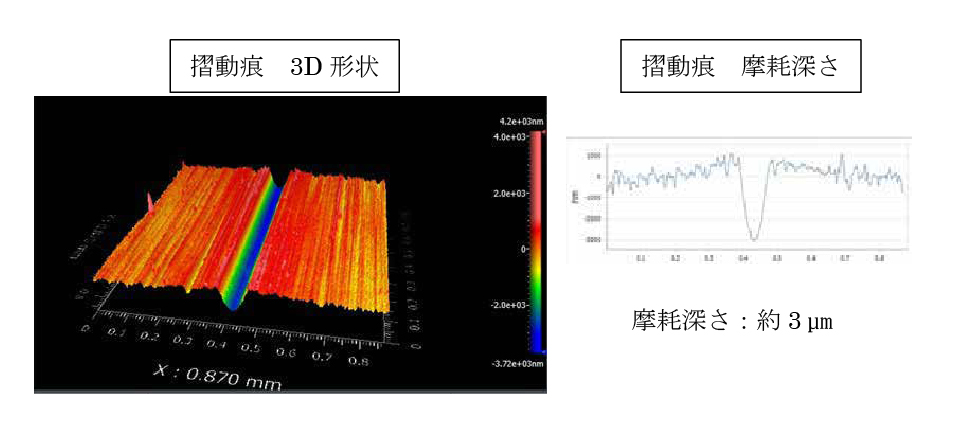
③ 硬さ試験機を用いた材料の硬度測定。
硬度は、耐摩耗性や耐擦傷性の評価を補完するデータとなる。(図7)
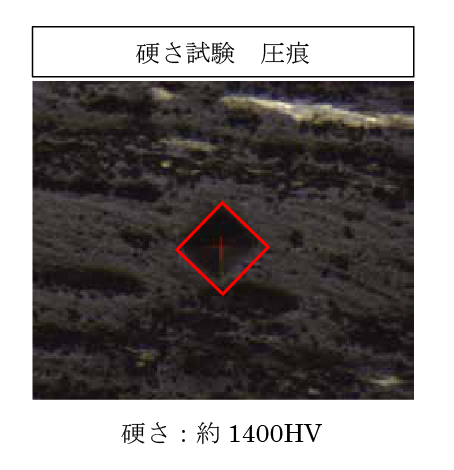
このように複数の試験機器を組み合わせて測定すれば、より精度の高い評価が可能となる。
6.摩擦摩耗試験方法のまとめ
各試験方法の特徴を表2 にまとめた。
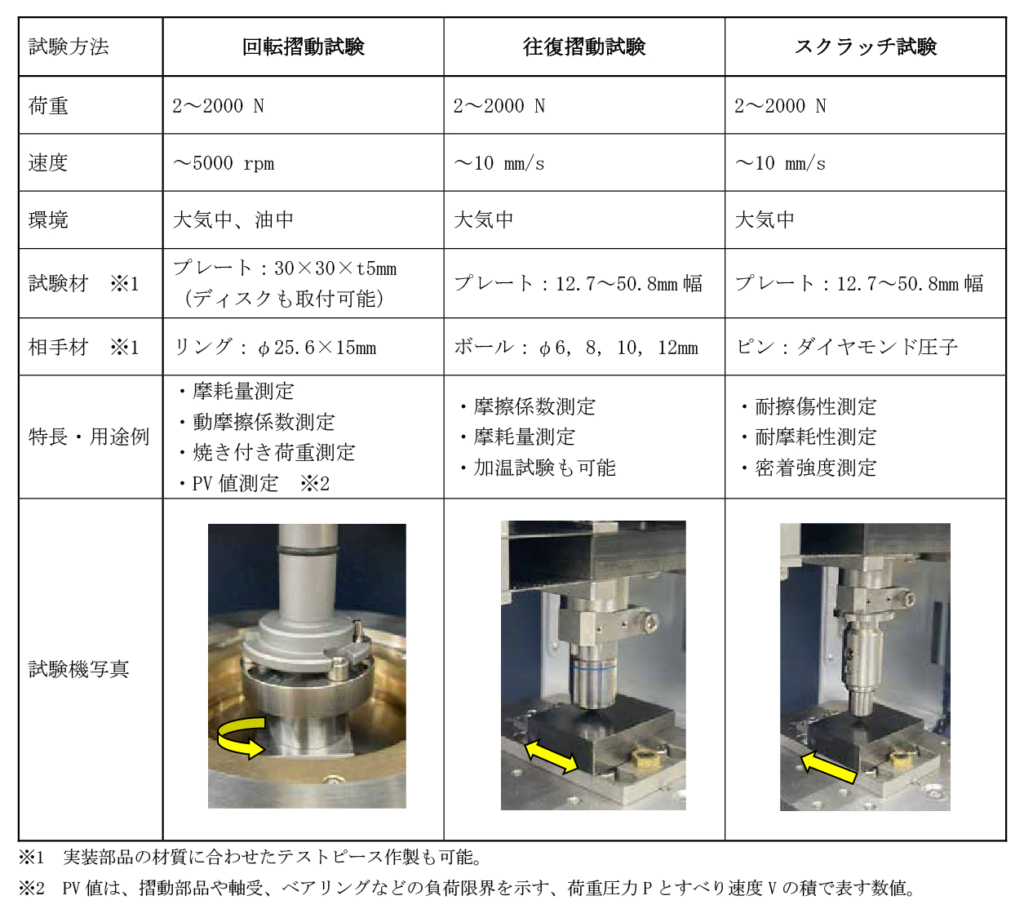
7.おわりに
トライボロジーの特性は、目的、材料の種類に応じて適切な試験条件を検討し、選定しなければ期待する正確な結果が得られず評価が難しい。試験を実施する場合、事前の詳細な情報提供と打合せが必須である。当社は創業以来多くの特殊分析を受託し様々な知見を蓄積しているため、ニーズに合わせたオーダーメイドの評価方法の提案が可能である。テストピースを用いた基本特性評価から実装部品の特性評価、数種類の分析手法を組み合わせた複合解析まで、トライボロジーに係る調査のご要望があればお気軽にご相談いただきたい。
参考資料
1) 中村隆.トライボロジー技術の進展による自動車の省エネ.トライボロジスト.2016,61(2),p.66.
2) 日本トライボロジー学会.トライボロジーは.https://www.tribology.jp/outline/shokai.html(参照2025-05-21)
3) 佐々木信也, 志摩政幸, 野口昭治,平山朋子, 地引達弘, 足立幸志, 三宅晃司. はじめてのトライボロジー. 講談社,2013,p.1-5,32,105,165,167.
4) 宮本勘史. カーボンニュートラル時代のトライボロジーの役割. いしかわ工試技術ニュース.2022,47(3).
5) ブルカージャパン.UMT TriboLab Mechanical Tester and Tribometer.[n.d.],[n.p.](. パンフレット)

皆様の記事の内容や分析に関してのコメントをお待ちしております。
※皆様から投稿いただいたコメントは公開させていただいております。
※弊社へのお問い合わせ(非公開)についてはこちらのフォームよりお願いいたします。
※は必須項目ですので、必ずご入力ください。
RANKING 人気事例ランキング
-
1
-
2
-
3
-
4
-
5
TAG LIST
